Top 9 Common Problem in Logistics Management

Many companies have already missed a plethora of logistics opportunities that could drive them toward growth.
Instead, they chose a supply chain that is full of errors. Therefore, it costs the company more money and time.
If your company’s supply chain isn’t optimized, chances are higher. It will increase the warehouse bulk, and the customers won’t get their goods at the specified time. It will also increase the overall expenditure related to your supply chain management.
In this blog, we will show you the mistakes you must avoid when it comes to goods transportation management for your company.
1. Inaccurate tracking of inventory
It is one of the most common problem warehouses make to keep accurate inventory records. This can lead to increased costs, lack of inventory balance, conflicting vendor customer relations, ineffective decision-making, decreased warehouse organization etc.
How to avoid inaccurate tracking?
Today’s warehouses must have a robust warehouse management system (WMS). It integrates the things like proper tracking and inventory management, receiving, shipping, reverse logistics etc. Integrating this system with other technology solutions like wireless headsets, mobile carts, and automated shelving, the workers’ productivity can be increased by 3X. Ultimately, it will reduce costs and save precious time.
2. Failure to optimize order-picking pathways
Overlooking the efficient picking pathways leads towards shrinking the picking rate. Therefore, it can impact the supply chain cycle times directly. Also, it can generate excessive labor costs due to suboptimal productivity.
How to avoid subprime order-picking issues?
Ensure you are optimizing the worker’s energy and time. Accordingly, it will help you to reduce wasted movement. You can also store the products, often bought together. Simultaneously, encourage your employees to use mobile handsets during the picking process. It will make the process seamless and hassle-free.
3. Poor planning issue
You may have curated a plan and incorporated the same in logistics management for your company. However, there is no hard and fast rule; the same will work again. With the evolving new technology, things are changing rapidly within this logistics industry. If you neglect the planning now, it will cost you a fortune in the future.
If the supply chain strategy isn’t robust and ready to adapt to the new changes, then it may not grow as per your organization’s needs. Moving forward, the chances of outperforming your competitors will diminish gradually.
How To Manage Planning Issues?
Evaluate the warehouse processes at least once or twice a year. Review the efficacy levels as per previously set parameters. It will help you find the glitches. In other words, the missed opportunities will be evident. Accordingly, make a robust plan to change the operations for a better future. For example, you can make a long-term growth plan to facilitate the supply chain once your company grows.
4. Inadequate staff training
Tight budgets and time constraints are two primary factors for not providing the required training. Sending the workers to the warehouses without proper training could be a recipe for disaster. Therefore, it can lead to more inefficient working results. It involves low success score of delivery, excessive usage of resources without knowing the procedure of execution, increased agitation of end users due to delayed delivery etc.
Suboptimal performance of these workers affects the entire supply chain eco-system as they are the core strength when it comes to managing the system efficiently.
How To Eliminate Inadequate Staff Training Issues?
You need to invest in staff training. It must include the knowledge of proper system handling, understanding the work policy, performing the supply chain works efficiently, planning and segregating the work based on priority etc. It will improve the workers’ productivity by 2X.
Also, proper training lets your workers know that you care about them. Therefore, it would improve employee retention rates.
5. Fail To Measure The Scale Potential
Evaluating scale potential plays a crucial role in efficient logistics operations. Too much stock needs ample store space, which may include the charges of leasing a warehousing unit. On the other hand, less stock with ample storage may result in unnecessary expenses. Consequently, too little stock can also translate into lost sales.
How To Mitigate The Risk Of Losses?
You can employ the advanced system with a minimum and maximum reorder feature. It will send notifications to restock the inventory once the stocks get finished.
6. Uncleaniness of Warehouse
Dust accumulated on shelves and broken equipment indicates your warehouse hasn’t appropriately cleaned. The cleanliness of your warehouse may be congested, unsafe and unproductive. A warehouse without decluttering for a long time brings inefficiency, affecting the ecosystem of proper supply chain services.
How To Clean The Warehouse?
You can create the housekeeping schedule after every employee shift. Also, deep cleaning must take place periodically.
7. Having too much inventory
Holding excess inventory can stand out as costly. Excess items that don’t sell within the stipulated time may expire or become obsolete. It is highly applicable to perishable goods. Also, too many items will clutter your warehouse, followed by making it less efficient.
How to avoid excess inventory issues?
You need to reduce your inventory level. You can do this by receiving larger orders in smaller batches.
8. Having items understocked
Besides holding excess inventory, understocking best-seller items is also bad. Once you face frequent stockouts, your consumers will get frustrated with the bad shopping experience. They will search for a competitor who can meet their demands.
How To Manage This Issue?
You can use analytics to track your inventory and sales. Also, you can trigger automatic reordering once the stock levels reach a predetermined level. Therefore, you will never run out.
9. Poor customer service
Customer service that involves pre and post-sales service must serve your customers properly by addressing and resolving their issues quickly. Poor customer service may hurt your business image. It will make the customers agitated. Chances are higher that they will go to your competitors to purchase their desired product/service.
Both customers and vendors play a crucial role in your organization’s success. Creating cordial bonding on both ends of the supply chain would help you the most when it comes to benefiting your company. The better you share the bonding with them, the better result supply chain management will produce.
How To Provide Excellent Customer Service?
You can set up a team of efficient customer reps. Ensure you provide them with the required training in order to interact with the customers with utmost efficiency. You can use the “CRM or customer relationship management” tool, which combines software, business strategies and practices to analyze customers’ data. It helps to build long-lasting relationships with customers.
Final Thoughts
Did you catch the ultimate goal? It all rests on eliminating logistic management problem to keep your organization running smoothly. Also, introduce these points to your team so that they can avoid making these mistakes. Afterall, you don’t want a catastrophic situation for your company’s reputation.
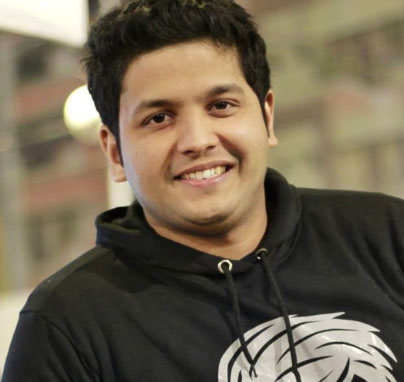
A content writer who dwells on writing while finding new adventures around words. Having experience working for SaaS and start-ups, I found the unwavering will inside me to meet new people, develop new relationships, solve issues and contribute to their business growth.